How Do You Get to Carnegie Hall? The Basics of Welding, Part 3
Practice! Now that you’ve learned the basics of welding in the previous two articles, on to the welding! One does not need to be a metallurgist to understand welding, but the basic metal properties need to be known. The first step to welding is to decide what metal and what type of weld to perform. For the purpose of this article, the weld will be a lap weld and the metal will be steel plate. The welding machine will be a mig welder with an inert gas. Although varied thicknesses of metal can be welded together, keeping the same thickness yields a better result. Use eighth inch steel plate as the practice material.
Two pieces of scrap eighth inch steel are cut into four inch by four inch squares. The metal must be prepared before attempting the weld. A small angle grinder can be used with a wire brush, flap disk or abrasive stripper. Clean the metal until it is bare and generally oil-free. Using vice grips or welding clamps, clamp the two pieces together with about a two inch over hang.
It is very important to adjust the welding machine settings, such as heat and space, before you start welding. Most welding machines have a chart inside the wire spool flap that gives adjustments to the varied thicknesses of metal. Remember a good weld will have good penetration. If the heat is too high, the weld will burn through the metal. If the heat is too low, there will not be enough penetration and the weld will break. Speed will control the flow of the metal. Slow speed can create gaps in the weld. High speeds will create puddles of weld. It is all a matter of trial and error. Adjust the settings until the best weld is created.
The welding machine has a ground clamp and an Argon/Co2 mix regulator. Attach the ground clamp to the metal which can be supported in a vise. Open the Argon/Co2 mix regulator. Make sure to wear protective clothing like leather gloves and a welding apron. Most importantly, a welding mask has to be worn to shield a person’s eyes. Flash burn is a common problem with welders that choose to weld with no mask. Permanent eye damage can come from this! Place the welding gun to the area that is being welded. Hold the tip about a half inch away from the metal joint. Flip the mask down and press the trigger!
This site and articles contained herein are provided for general informational purposes only and are not a substitute or intended as professional advice. Please be sure to refer to your owner’s manual or consult a mechanic for information specific to your motorcycle. The information contained on this site and articles contained herein are provided on an “as is” basis with no guarantees of completeness, accuracy, usefulness or timeliness and without any warranties of any kind whatsoever, express or implied. Rider Insurance Company and its affiliates (together, “Rider”) assume no responsibility for any errors or omissions in the content of this site and articles contained herein. Any action taken upon this information is strictly at your own risk and Rider will not be liable for any losses or damages in connection with your use of this site and articles. Additional terms and conditions apply and are available at https://www.rider.com/plymouth-rock-assurance-general-terms-and-conditions/.
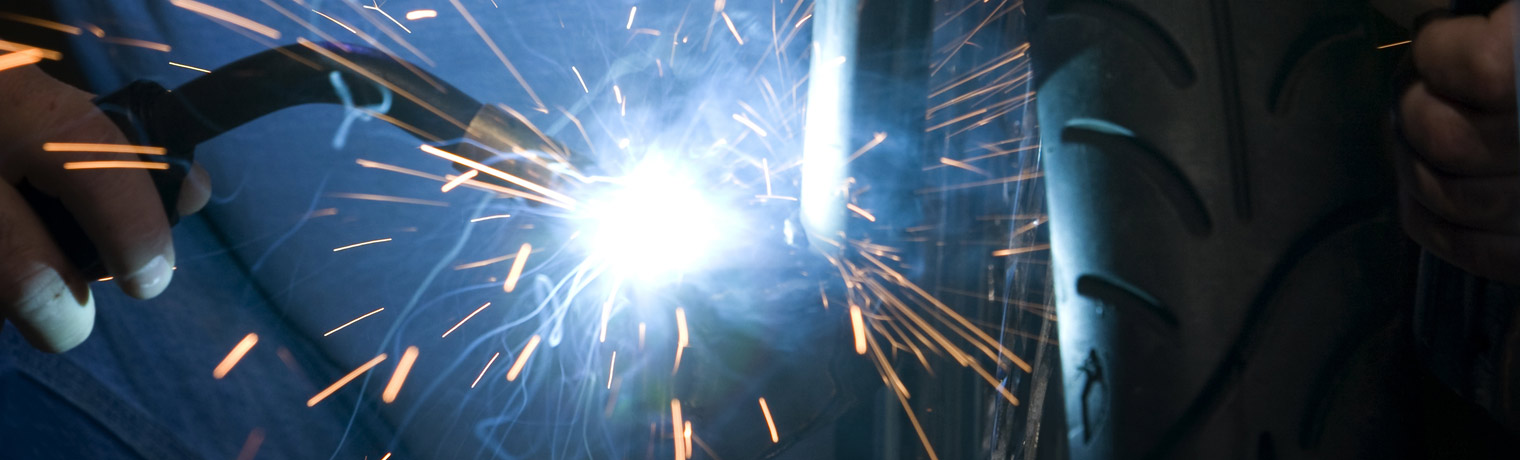
Do not push the gun to contact the metal directly; let the wire come out of the gun. Continue to hold that half inch gap from the steel. To create a tack weld, move in a short circle and stop after about two seconds of welding. This will form a small dot of weld on the metal, and now the two pieces of steel are fused together. To create a bead of weld do exactly the same and continue to form a line of circles. Overlap the next circle while moving down the joint to create one continuous bead. Through the mask the metal will look molten or as if the edge is burned off the steel plate. It’s pretty amazing that one can see the metal fusing together.
Once the welding is finished, it should look like a stack of dimes laid down. Figuratively of course, because a stack of dimes would be quite a large weld. Some people use different methods, like making figure eights and going from side to side. However, the way the welding gun is used affects the aesthetics of the weld. The electric zap of the weld should have a consistent sound throughout the weld. If it sounds like it is sputtering, the welding machine has the wrong settings. They should be adjusted properly or else the weld will be inconsistent and spotty. Of course, the metal will be very hot, so do not touch it with bare hands. The metal around the welded area should be blue in color. The blue occurs because of the heat transfer. If it’s not blue, the weld might not have been hot enough. A little cleaning with a wire brush and the weld should be good. The great thing about metal is if the weld doesn’t look good, it can always be grounded down smoothly and welded again.
Lap joint and T-joint welding are easier to practice because the risk of burning through is very low. Butt joint and V-Butt joints prove to be harder because there is no backing of the other material, which causes a greater risk of burning through. When practicing any kind of butt joint, the space between the joint is very crucial. A general rule of thumb: the space between two metals should be as large as the thickness of the metal. The general idea of Butt joint welding is the same as lap welding. It is very easy to warp a Butt joint. Stitch welding is welding first high on the joint, then low, then high again and so on. This lets the heat dissipate faster, which helps minimize the warpage of the steel. When welding a thick plate warpage is less evident in continuous beads than it is when welding very thin metal.
There are many more techniques to welding, but that would require a book to cover it all. Stick welding has completely different techniques than gas welding. Welding can be done underwater and in outer space. Molten welds can be hammered down and formed. Welding is performed by humans and robots. There is a lot going on in the world of welding. It is a great skill a do-it- yourselfer can obtain. Whether you’re fixing a hand railing or building a custom chopper, welding is a very useful tool!
Plymouth Rock Assurance is a marketing name used by a group of separate companies that write and manage property and casualty insurance in multiple states. Motorcycle insurance in New Jersey and Pennsylvania is underwritten by Rider Insurance Company. Each company is financially responsible only for its own insurance products. Actual coverage is subject to the language of the policies as issued by each separate company.