Customization With Custom Headlights
Customization can really personalize your bike and turn it into a one of a kind statement in line with your own style and personality. Custom pipes, handlebars, wheels, or paint can radically transform a stock motorcycle. The devil is in the details though, and I want to recommend that you pay attention to one very cool and often overlooked detail: custom headlight and headlight set-ups. You may not have considered this in your customization plan, but they can really complete your overall look. Headlights come in a variety of shapes and sizes, available from either original or aftermarket manufacturers.
So many to choose from…
There are a vast number of headlight options for all different types of motorcycles. Manufacturers tend to use a built-into fairing headlight for sport-style motorcycles. A bullet shaped chrome or black headlight is common on cruisers and LEDs, and Xenons are definitely becoming hits with newer models. Manufacturers like Harley-Davidson and Suzuki are already using LEDs in some of their models. Xenon and projector (glass eyes that reflect more intense light) head beams can be found in a lot of sport bikes already.
Getting started with aftermarket headlights
Customizing headlights can be as simple as swapping them with different ones. A lot of aftermarket companies make custom headlights. These headlights are usually offered with a bracket so that no fabrication is needed. Most of these types of headlights are very easy to install. They usually require only a small number of tools. A set of Allen keys (usually metric) and a set of open-end wrenches can usually get the job done. Some headlight manufacturers prewire the headlight to just plug into a stock wiring harness. Some universal applications may require cutting and splicing the wires.
This site and articles contained herein are provided for general informational purposes only and are not a substitute or intended as professional advice. Please be sure to refer to your owner’s manual or consult a mechanic for information specific to your motorcycle. The information contained on this site and articles contained herein are provided on an “as is” basis with no guarantees of completeness, accuracy, usefulness or timeliness and without any warranties of any kind whatsoever, express or implied. Rider Insurance Company and its affiliates (together, “Rider”) assume no responsibility for any errors or omissions in the content of this site and articles contained herein. Any action taken upon this information is strictly at your own risk and Rider will not be liable for any losses or damages in connection with your use of this site and articles. Additional terms and conditions apply and are available at https://www.rider.com/plymouth-rock-assurance-general-terms-and-conditions/.
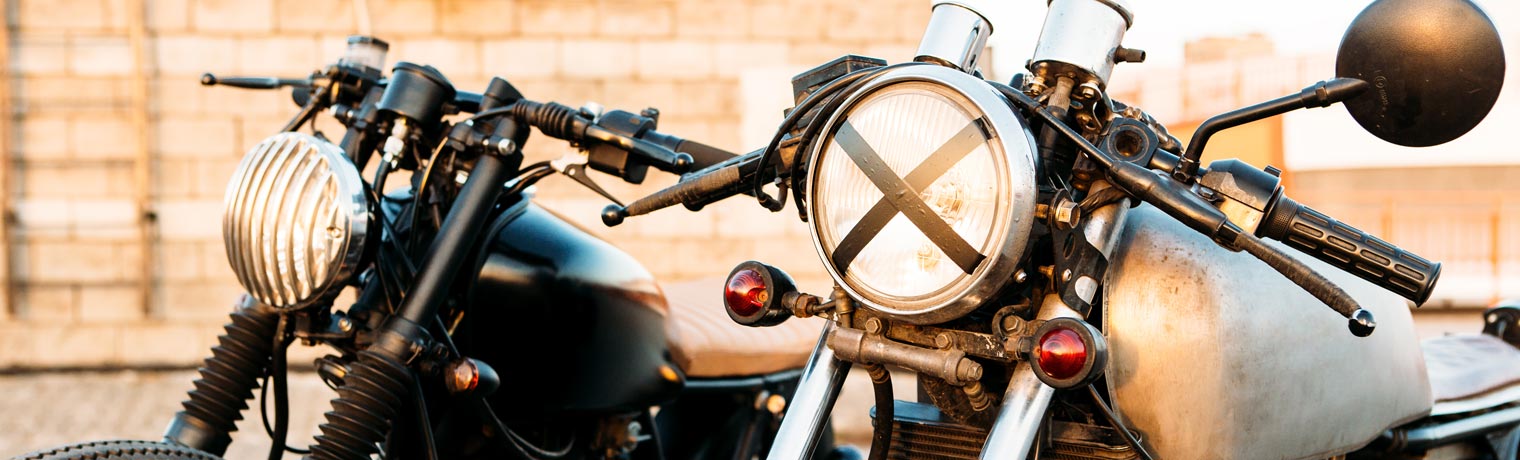
Wiring basics
The basics of wiring are simple. First, before any cutting or unplugging of wires, disconnect the negative terminal of the battery. Next, get the lay of the land: a headlight that has a high and low beam will usually have three wires. One wire will go to the high beam and one wire will go to the low beam. The third wire is a ground wire, which is usually attached to the body of the headlight. You may also find that some headlights may not have ground wires because the body itself acts as the ground. As long as there is metal to metal contact with the headlight, this method will work just fine.
Splice and Dice
Cutting and splicing wiring may seem daunting, but don’t worry; it’s easier than you think. A good pair of wire-cutting pliers will do the trick. Just cut the wire. Make sure there is enough for slack before cutting the wire. Your wire cutter will have stripper shears attached. These will cut through the casing of the wire, but not the wire itself. Find the correct gauge of wire and use the corresponding size strippers. Leave about a half-inch of bare wire. Twist all the wire strands together to form a strong wire end.
There are different types of connections that can be used when splicing wires. A butt connector will connect two wires together through a crimped connection. Female and male spade connectors, as well as female and male bullet connectors, are also crimped on but they can be quickly disconnected. This works well if you need to separate the wires in the near future.