Wow, That’s Bright! The Basics of Welding, Part 2
This is the next article in the welding series. First and foremost, the actual welder will either need to be purchased or borrowed. Respectable brands usually yield good results. A typical flux core mig welder can run from $200 to $500, while an argon shield mig welder can go from $400 to $2,000. Tig welders are quite expensive and can get into the thousands of dollars. Other things needed before welding include a welding helmet, gloves, a wire brush, an angle grinder, a hammer and pliers. Some welders come with helmets, but helmets are another item that can get expensive. One great feature some welding helmets have is an auto darkening feature. Early welders would have to flip the mask down while welding and then flip it up to see what was done. Auto darkening helmets have an electric shade that automatically comes on when welding and turns off when welding is finished. A foolish way to weld is with no shield at all. Some people think if they close their eyes they will be fine. That is not true and is very dangerous. Welding emits light brighter than looking into the sun. Professional welders tend to get flash burn, which is like sun burn on the eyes. A person closing one’s eyes is still at risk to this light, because it passes through the eyelids and burns the retina. For safety reasons, please wear a welding mask!
Two dissimilar metals cannot be welded to each other. This means metals such as aluminum and steel cannot be welded to each other because of their metallurgy. However, metals of different thicknesses can be welded to each other. The thickness of the metal determines how hot and fast the weld needs to be. Stick welding is used on very thick metals because it carries a lot of amps (measure of electric current). The amps are needed to penetrate the thick metal. Unfortunately, welding sheet metal with a stick welder is tricky because it tends to burn through. Mig and tig welders can weld varied thicknesses of metal. Sheet metal is measured in gauges like wire. A good start to practice welding thin metal is 20g to 18g sheet metal. Many manufactures make clamps and pliers to hold sheet metal in place. Welding pliers are generally known as vise grips with a long reach. Some welders make jigs, which are essentially position holders. The metal can be placed in a jig and welded the same, time after time. Jigs work very well when welding motorcycle frames.
This site and articles contained herein are provided for general informational purposes only and are not a substitute or intended as professional advice. Please be sure to refer to your owner’s manual or consult a mechanic for information specific to your motorcycle. The information contained on this site and articles contained herein are provided on an “as is” basis with no guarantees of completeness, accuracy, usefulness or timeliness and without any warranties of any kind whatsoever, express or implied. Rider Insurance Company and its affiliates (together, “Rider”) assume no responsibility for any errors or omissions in the content of this site and articles contained herein. Any action taken upon this information is strictly at your own risk and Rider will not be liable for any losses or damages in connection with your use of this site and articles. Additional terms and conditions apply and are available at https://www.rider.com/plymouth-rock-assurance-general-terms-and-conditions/.
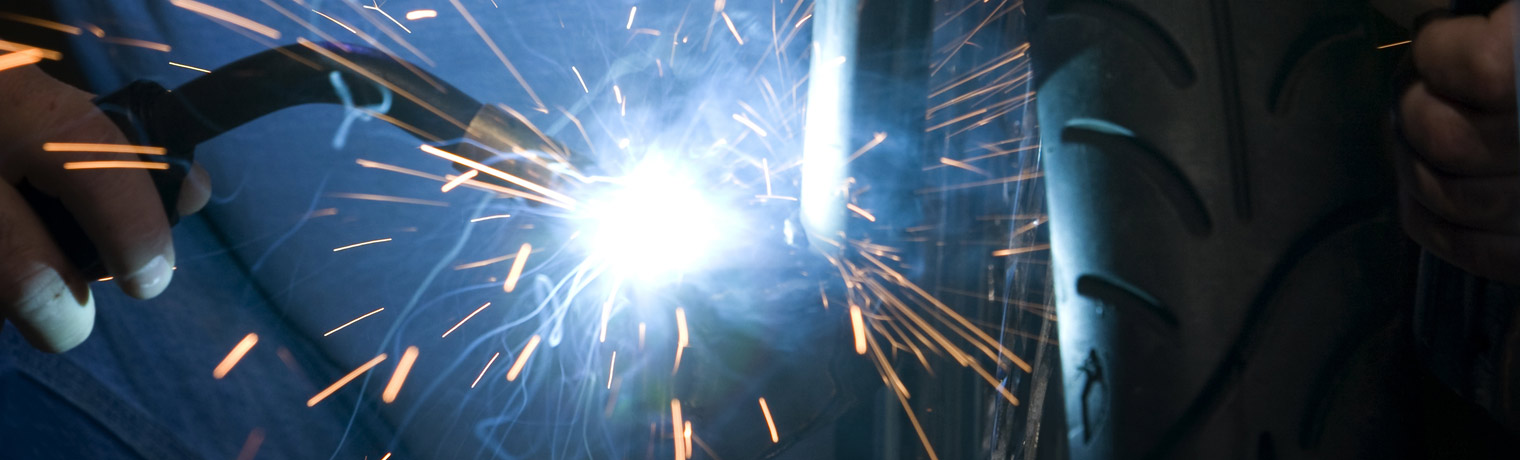
There are different types of joints for welding. Taking two pieces of metal and butting them up to each other is called a butt weld. Laying one piece of metal over the other is called a lap weld. Lap welds tend to be stronger because there are two pieces of metal supported underneath each other. Unfortunately, metal cannot be lapped in every case. Another type of welding is plug welding. For example: A frame tube of a motorcycle is wrecked and needs to be replaced. Taking two pieces of rolled tubing and butting them up against each other seems like the most logical solution. However, this is not the right way. (In some applications when the stress of weight is not pushing down at every instance, this may apply.) A motorcycle frame sees a lot of stress from weight. Rather than just butting two tubes against each other, a slug is inserted inside of the tube. A slug is a solid piece of metal just smaller in diameter to fit inside the tube. It would, however, be impossible to hold in place when the tubes are butted against each other. A hole is drilled through the tube but not the slug. A weld can then be applied inside the hole to the slug. This holds the slug in place and then it can be solidly welded around the tube. Welding through a hole is called plug welding.
Spot welding, which is something common on cars, actually uses no welding wire. A machine uses pressure and heat to fuse metal panels together. It forms a little spot; hence spot welding.
Getting excited yet? There are formal teachings of welding at colleges and trade schools. Some people find it too expensive to go out and buy a welder. Welding can be practiced in these classes before a welder would actually have to be purchased. The next article will get into welding and practice. Stay tuned for more of the welding adventure!
Plymouth Rock Assurance is a marketing name used by a group of separate companies that write and manage property and casualty insurance in multiple states. Motorcycle insurance in New Jersey and Pennsylvania is underwritten by Rider Insurance Company. Each company is financially responsible only for its own insurance products. Actual coverage is subject to the language of the policies as issued by each separate company.